CNC Maintenance | PLC Troubleshooting Flowchart
- Home >
- articles >
- automation >
- cnc maintenance plc troubleshooting
Machine Operator to Maintenance Technician.
Click twice on Fig 1 to zoom in on the PLC troubleshooting flowchart for CNC operator level to maintenance and PLC.
This CNC PLC troubleshooting flowchart example is when the CNC machine won't start due to the 'Safety Door Not Closed' indicator on the CNC operator control panel. From machine operator level CNC troubleshooting to maintenance technician PLC troubleshooting, this CNC - PLC troubleshooting flowchart will help to understand the process.
CNC Operator:
Some CNC operators perform the initial maintenance technician troubleshooting steps above. The majority of operators conform to the above flowchart. The CNC operator is typically limited to the limited control access a CNC controller provides in the CNC operator control panel. In contrast, maintenance can access complete control and perform PLC troubleshooting.
- Visual Inspection (Is the CNC door closed?)
- No?
- Close the Door, and Try Again.
- Yes?
- Close-up visual inspection of CNC door safety sensor.
- Did the sensor need to be tightened or adjusted?
- Yes?
- Close the Door, and Try Again.
- No?
- Call Maintenance
- Yes?
- No?
Maintenance Technician:
The maintenance technician job description (or field service technician) is to troubleshoot at a more complex level to determine faults with wiring, devices, and communication issues between even more complex control devices (CNC PLC). The maintenance technician with proper PLC training uses the PLC (Programmable Logic Controller) to make troubleshooting about 80% quicker and easier, referred to as "PLC Troubleshooting". There are additional steps within the basic steps shown in the above PLC troubleshooting flowchart. We are just simplifying the flowchart for illustration purposes.
- Is the "Door Closed" sensor signal getting into PLC? (PLC LED or Ladder Logic)
- Yes?
- [2] Is the "Door Closed" signal getting to CNC from PLC?
- No?
- Check the "Door Closed" bit in the Message or Output card wire sent from PLC to CNC. If "No", trace back in the PLC program and wiring accordingly.
- Yes?
- Seek CNC vendor support. There may be an additional input or M-code required for the CNC operator control panel to indicate "Door Closed".
- No?
- [2] Is the "Door Closed" signal getting to CNC from PLC?
- No?
- Check voltage at PLC input screw.
- Yes?
- Is the "Door Closed" Signal getting from PLC to CNC?
- No?
- Check the "Door Closed" Bit in the Message or output card wire sent to the CNC.
- Yes?
- Call the CNC vendor.
- No?
- Is the "Door Closed" Signal getting from PLC to CNC?
- No?
- Check the voltage at the CNC door sensor output.
- Yes?
- Check the wiring between the CNC door sensor and the PLC.
- No?
- Check the voltage at the input to the CNC door sensor.
- No?
- Check the power source to the CNC door sensor.
- Yes?
- Replace the CNC door sensor.
- No?
- Check the voltage at the input to the CNC door sensor.
- Yes?
- Check the voltage at the CNC door sensor output.
- Yes?
- Check voltage at PLC input screw.
- Yes?
PLC Troubleshooting:
Most "CNC Maintenance" and even "CNC Troubleshooting" courses or sections in CNC manuals do not even include PLC Troubleshooting. But as you can see from the CNC PLC troubleshooting flowchart example above, the PLC is an integral part of CNC control. The CNC controller works with the PLC controller to complete the whole process.
While PLC training has always been a critical part of the maintenance technician job description, as machine operator jobs evolve to be more technical and include some maintenance, PLC troubleshooting on a low level can significantly reduce downtime. Using troubleshooting flow charts like the one on this page, you can customize it to include more of the minor stages of PLC troubleshooting for the machine operator to perform. They will need the PLC Technician Training Software Bundle to build their technical knowledge and sharpen their troubleshooting skills in that approach.
For example, a CNC operator or, for that matter, any machine operator could perform the troubleshooting steps that only require looking at PLC input and output LEDs on the face of the PLC. (not hooking up a computer to PLC to monitor the PLC program as that gets into the maintenance technician level and they need proper PLC training for that.) Also, many sensors, like the CNC door sensor in this example, often have an LED on them to indicate whether they are triggered. So, a CNC operator would not need to learn how to use a multi-meter for a quick low-level check of the sensor.
For the maintenance technician, though rare, PLC troubleshooting can get complicated, especially when it is a PLC CNC communication issue. Questions arise about system design. For example, is the CNC controller sending feeds and speed to the PLC, which sends them to Servo drives? It gets even more complicated if a PAC motion control is used instead of a PLC. Or with a particular CNC, the PAC is built into the CNC controller, sending feeds and speed directly to Servo drives and using RIO for door closed signal, etc.
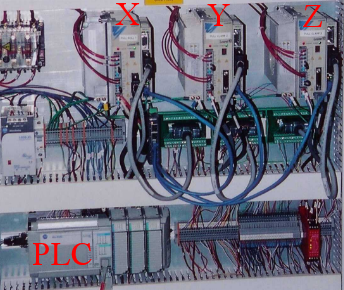
Raise your machine operators' and CNC operators' maintenance skills level with the Autonomous Maintenance Training Program (Phase II).
About the Author: Don Fitchett founded the activity-based costing system called "True Downtime Cost"™ (TDC), authored books and spoke at conventions on the topic, and is president of BIN. Don has been in the industrial training sector for over two decades, setting up training programs worldwide, and still conducts onsite PLC training workshops to stay current.
Copyright 2023 BIN95.com (You may link to this article only)